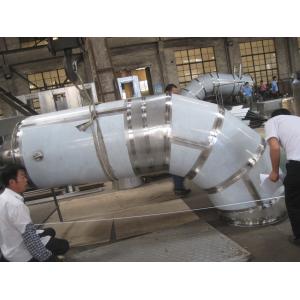
Add to Cart
Description of the Spray Dryer
This equipment is used to dry solid liquid such as solution and suspending liquid. In the tower, the materials can be heated in short time and evaporated quickly and the temperature of heat exchanger is lower so that it has little impact on the solubility, color, flavor and nutrition of the product. Therefore, this equipment is widely used in the industries of food, medicine and chemical products, especially suitable to dry the heat-sensitive materials by spraying such as thick milk, soy milk, egg liquid, blood meal, medicament, yeast and food additives.
Principle of spary dryer
Hot air by the inlet pipe to the suitable spouted velocity from the bottom of the dryer into the mixing crushed drying chamber, the material produce strong shearing, blowing floating and rotating effect, so the material by centrifuge, shearing, collision, friction and particles, and to strengthen the heat transfer and mass transfer. At the bottom of the dryer is bigger than the wet particle mass under the action of stirrer were mechanical crushing, with low moisture content, granularity of smaller particles entrained by the rotating flow increase, rising further in the process of drying. Because of gas-solid two phase rotating flow, solid phase of inertia is greater than the gas phase and two phases of gas in the relative velocity is larger, strengthen two heat transfer and mass transfer, so the machine produce high strength.
Preface
Spray drying is the technology most widely used in the liquid technology shaping and in the drying industry. The drying technology is most suitable for producing solid powder or particle products from liquid materials, such as: solution, emulsion, suspension and pump- able paste states. For this reason, when the particle size and distribution of the final products, residual water contents, volume density and the particle shape must meet the precise standard, spray drying is one of the most desired technologies.
After been filtered and heated the air enters into the air distributor on the top of the dryer. The hot air enters into the drying room in the spiral form uniformly. Passing through the high-speed centrifugal sprayer on the top of the tower, the material liquid will rotate and be sprayed into the extremely fine mist liquid beads. Through very short time of contacting the heat air, the materials can be dried into the final products. The final products will be discharged continuously from the bottom of the drying tower and from the cyclones. The waste gas will be discharged from blower.
Feature :
The drying speed is high when the material liquid is atomized, the surface area of the material will increase greatly. In the hot-air flow, 95%-98% of water can be evaporated at a moment. The time of completing the drying is only several seconds. This is especially suitable for drying the heat sensitive materials. Its final products own the good uniformity, flow ability & solubility. And the final products are high in purity and good in quality. The production procedures are simple and the operation and control are easy. The liquid with moisture contents of 40-60% (for special materials, the contents might be up to 90%.)can be dried into the powder or particle products once a time. After the drying process, there is no need for smashing and sorting, so as to reduce the operation procedures in the production and to enhance the product purity. The product particle diameters, looseness and water contents can be adjusted through changing the operation condition within a certain range.
ed centrifugal sprayer on the top of the tower, the material liquid will rotate and be sprayed into the extremely fine mist liquid beads. Through very short time of contacting the heat air, the materials can be dried into the final products. The final products will be discharged continuously from the bottom of the drying tower and from the cyclones. The waste gas will be discharged from blower.
Technical Data:
specification | LPG | ||||||
5 | 25 | 50 | 100 | 150 | 200-3000 | ||
Tep of inlet air | less than 350°C | ||||||
Tep of outlet air | 80-90 | ||||||
(kg/h) | 5 | 25 | 50 | 100 | 150 | 200-3000 | |
Transmitted | Compressed air | By machine | |||||
(rpm)Rotating speed | 25000 | 22000 | 21500 | 18000 | 18000 | 15000 | |
(mm) | 50 | 120 | 120 | 120 | 150 | 180-340 | |
Heat source | Electricity | Electricity | + | + Electricity+ steam | + Electricity+ steam, oil fuel, gas | Solved by customer | |
(kw) | 9 | 45 | 60 | 81 | 99 | ||
(%) | ≥95 | ≥95 | ≥95 | ≥95 | ≥95 | ≥95 | |
Installation Size for reference | A(mm) | 1000 | 1290 | 1730 | 2500 | 2800 | Decided in accordance with actual condition |
B(mm) | 2100 | 3410 | 4245 | 5300 | 6000 | ||
C(mm) | 2300 | 4260 | 4645 | 6000 | 6700 | ||
φ D(mm) | 1060 | 1800 | 2133 | 2560 | 2860 | ||
E1(mm) | 1050 | 1200 | 1640 | 2100 | 2180 | ||
E2(mm) | 1050 | 1200 | 1640 | 2100 | 2180 | ||
F(mm) | 750 | 1000 | 1250 | 1750 | 1970 | ||
G(mm) | 530 | 1700 | 1750 | 1930 | 2080 | ||
H(mm) | 530 | 1300 | 1800 | 2600 | 3050 | ||
I(mm) | 530 | 1550 | 1600 | 1780 | 1960 |