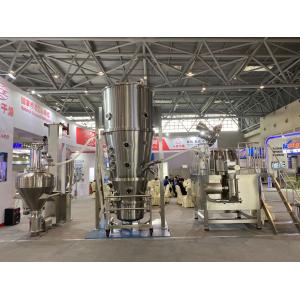
Add to Cart
Newly- designed solid dosage production line
DESCRIPTION:
Notes:
1. This kind of machine are made based on customized design. Not all the features are provided with all designs. The real configurations should be made as per the Contracts or Agreements signed.
2. The material for manufacturing the machine can be AISI304 ,316L and so on . It depends on the customer request.
3. For the heating method , it can be steam ,electricity ,gas-furnace and so on .
Production process flow for the newly-designed solid dosage production line
Production process flow chart 1:
After weighing, the materials are inhaled into High speed Wet Mixing Granulator through vacuum feeder, at the same time, the adhesive from the liquid tank is atomized into the high speed mixing granulator by Pressure spray gun, then mixes with fine powder and become soft material. By the force of the cutting knife , the soft material become wet granule . through the wet mill , the wet granule will become uniform .the uniform wet granule enters the dryer to dry by the vacuum negative pressure .the dried granule will discharge out by the vacuum discharger . the dried granule will be established the size through the dry mill . After that, the qualified dried granule will enter the hopper mixer for general mixing by the vacuum discharger .then they can continue other processes.
Production process flow chart 2:
After weighing, the materials are inhaled into High speed Wet Mixing Granulator through vacuum feeder, at the same time, the adhesive from the liquid adding tank is atomized into the high speed mixing granulator by Pressure spray gun, then mixes with fine powder and become soft material. By the force of the cutting knife , the soft material become wet granule . through the wet mill , the wet granule will become uniform .the uniform wet granule enters the vertical fluid bed dryer to be dried by the vacuum negative pressure .the dried granule will discharge out by the vacuum discharger . The dried granule will be established the size through the dry mill. After that, the qualified and dried granule will enter the hopper mixer for general mixing by the hopper lifter .then they can continue other processes.
After weighing, the materials are inhaled into High speed Wet Mixing Granulator through vacuum feeder, at the same time, the adhesive from the liquid adding tank is atomized into the high speed mixing granulator by Pressure spray gun, then mixes with fine powder and become soft material. By the force of the cutting knife , the soft material become wet granule . through the swaying granulator , the wet granule will become uniform .the uniform wet granule enters the dryer to dry by the vacuum negative pressure .the dried granule will discharge out by the vacuum discharger . The dried granule will be established the size through the dry mill. After that, the qualified dried granule will enter the hopper mixer for general mixing by the vacuum discharger .then they can continue other processes.
Features of newly-designed solid dosage production line
1. In traditional granulating and drying technology, each device is set in separate rooms, so the material transfers between different purification rooms, which can’t avoid the secondary pollution phenomenon. While the newly-designed solid dosage production line adopts the way of airtight transportation, ensuring the granulating and drying to complete in the same purification room, which may avoid the secondary pollution and make the granulating and drying process more scientific and reasonable, besides, this reduces space the equipment covers and make the process meet better with the GMP requirements.
2.This machine takes full consideration of compatibility between systems. Users can adjust corresponding equipment according to customer's actual capacity and dosage forms to make the production process achieve the optimum allocation, so as to ensure the continuity and stability of the production.
3. The user can separately storage, collect and print the technical data of the Wet granulation system and Fluidized dry granulation system through the HMI. The user can also control the parameter setting and monitoring of several sets of equipment through a control cabinet, besides, all the parameters can be set and modified, and the user can set multilevel password through the corresponding level. The main menu of the control system can reflect the working state, data statistics in real time, and reflect the equipment failure situations by fault self-diagnosis system and alarm records, which makes the production process fully automatic, and ensures the process stability.
4. The machine is able to fully show off the advantages of wet granulator and Fluidized granulator. Besides, this combination can guarantee high grain yield.
5. Vacuum feeder and turnover lifter have high automatic production capability, which may take place traditional manual operation, correspondingly reduce the labor intensity and dust pollution.
6. We can equip cleaning-in-position in many different points according to user requirements, which makes CIP cleaning more reliable.
YIBU provides advanced documentation support for you