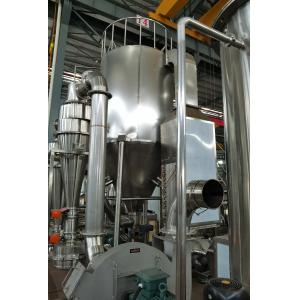
Add to Cart
LPG Series milk powder Centrifugal Atomizer Spray Dryer/Egg Powder Extracting Spray Drying Machine /Egg Powder Water Evaporating Dehydrator
Description:
Spray drying process is the widest used in the liquid forming process and in drying industry. The drying technology is most suitable for powder, particle products from materials, such as,solution, emulsion, SC and pumpable paste states material. For this reason, when the particle size and distribution of the final product, their residual water contents, the stacking density and particle shape must meet the precision standard, spray drying process is one of the most desired processes.
Feature:
High drying speed atomizes material into liquid, the surface of the material increase greatly. It only takes few seconds to evaporate 95-98% water in a hot air flow. This is especially suitable for drying the heat sensitive materials. The final product has features of good uniformity, flow ability, and solubility. It is in a high purity and quality as well. The production procedure is simple,operation and control are easy. For material contains 40-60% water(special material can contain more than 90%), it can be dried into powder or particles once a time. After the drying process, there is no need for smashing and sorting, so as to reduce the operation procedures in the production and to enhance the product purity. The product particle diameters,losseness and water contents can be adjusted through changing the operation condition whining a certain range. It is very convenient to carry out control and management.
Application:
Food and plants: Oats, chicken juice, coffee, instant tea, seasoning spices meat, protein, soybeans, peanut protein, hydrolysates and so on.
Carbohydrates: Corn steep liquor, corn starch, glucose, pectin, maltose, potassium sorbate and the like.
Chemical industry: Battery raw materials, basic dye pigments, dye intermediates, fertilizer, formaldehyde silicic acid, catalysts, agents, amino acids, silica and so on.
Ceramics: Alumina, ceramic tile materials, magnesium oxide, talcum powder and so on.
Technical Data
specification | LPG | ||||||
5 | 25 | 50 | 100 | 150 | 200-3000 | ||
Tep of inlet air | less than 350°C | ||||||
Tep of outlet air | 80-90 | ||||||
(kg/h) | 5 | 25 | 50 | 100 | 150 | 200-3000 | |
Transmitted | Compressed air | By machine | |||||
(rpm)Rotating speed | 25000 | 22000 | 21500 | 18000 | 18000 | 15000 | |
(mm) | 50 | 120 | 120 | 120 | 150 | 180-340 | |
Heat source | Electricity | Electricity | + | + Electricity+ steam | + Electricity+ steam, oil fuel, gas | Solved by customer | |
(kw) | 9 | 45 | 60 | 81 | 99 | ||
(%) | ≥95 | ≥95 | ≥95 | ≥95 | ≥95 | ≥95 | |
Installation Size for reference | A(mm) | 1000 | 1290 | 1730 | 2500 | 2800 | Decided in accordance with actual condition |
B(mm) | 2100 | 3410 | 4245 | 5300 | 6000 | ||
C(mm) | 2300 | 4260 | 4645 | 6000 | 6700 | ||
φ D(mm) | 1060 | 1800 | 2133 | 2560 | 2860 | ||
E1(mm) | 1050 | 1200 | 1640 | 2100 | 2180 | ||
E2(mm) | 1050 | 1200 | 1640 | 2100 | 2180 | ||
F(mm) | 750 | 1000 | 1250 | 1750 | 1970 | ||
G(mm) | 530 | 1700 | 1750 | 1930 | 2080 | ||
H(mm) | 530 | 1300 | 1800 | 2600 | 3050 | ||
I(mm) | 530 | 1550 | 1600 | 1780 | 1960 |